Bow Junction in Lockdown
Peter Mann
5th July 2020
2 minutes
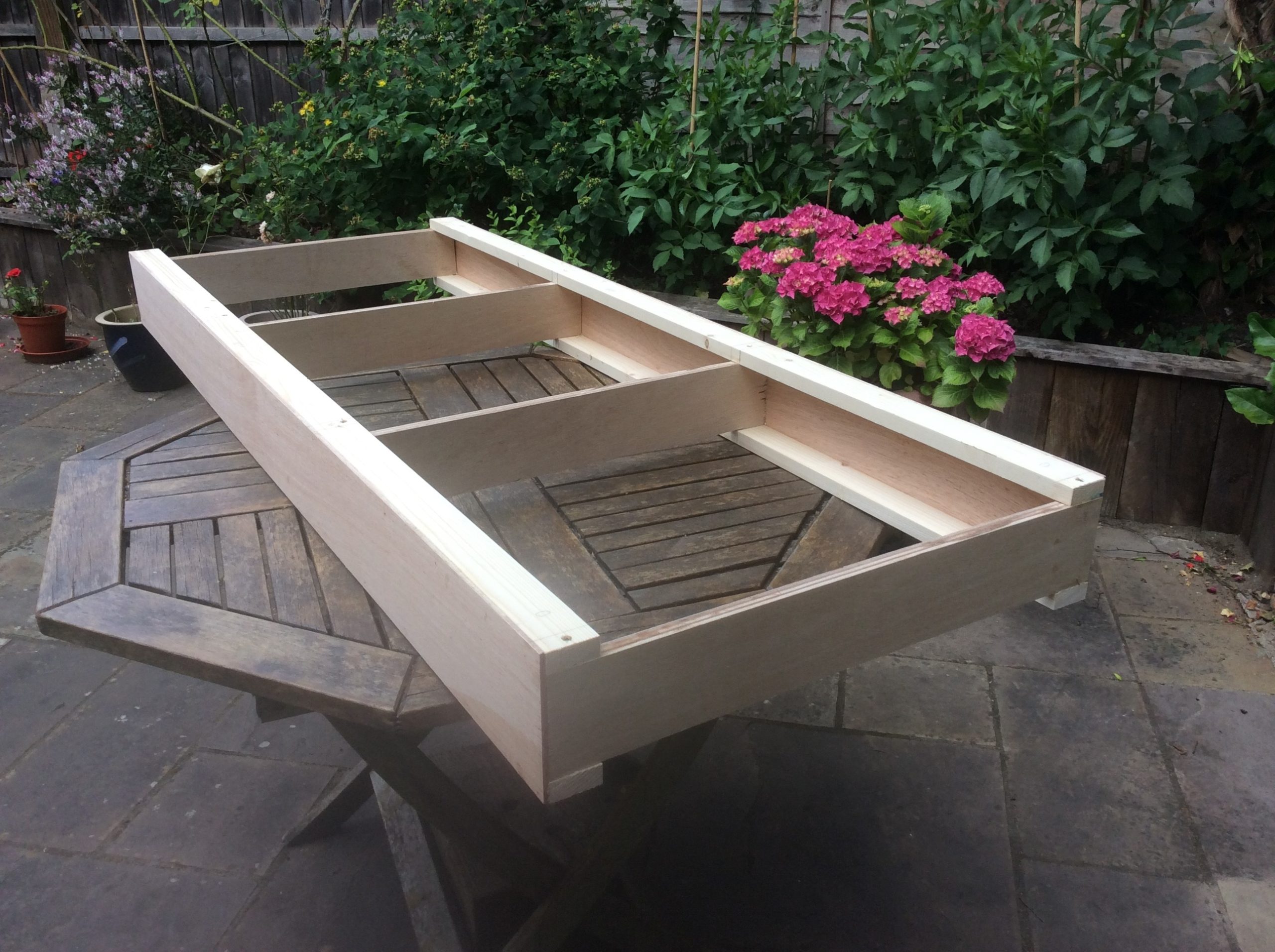
Along with everyone else, when lockdown was announced we simply stopped meetings at Keen House, and the layouts were left as they were. For Bow Junction, that meant set up in our lower hall, with the track making good progress as shown here:
And here’s the work on the trackwork into the shed
And that it is until today – sat there, silently in the middle of the room gently gathering a fine layer of dust.
You may have seen that work has continued on some of the buildings, but we’re at the stage now where we really need to think about the fiddle yard boards and connecting them to the layout. Work on the baseboards has started at home, and this sequence shows the first support board under construction
Here’s the pivot for the sector plate fixed in place.
Now that lockdown is easing, whilst we can’t yet meet properly at Keen House, we feel able to travel and take some sections of projects home, and today two of us will be at Keen House taking down the layout (safely) to be able to take relevant boards home and connect up the fiddle yard structurally, then start to lay the track.
The next stage is to make the moving part of the sector plate which will be made from a sheet of 12 mm ply. Further details will come when we have completed more work.
If you want to get involved with the exciting project, join today, and if you are already a member get in touch with me, details in The Bulletin.
2 thoughts on this post
Leave a Reply
You must be logged in to post a comment.
Thursday Track Nights
We are open on Thursday evenings from 7pm to 9pm at our Keen House clubrooms. Visitors are welcome, please come along and introduce yourself.
Address:
Keen House, 4 Calshot Street, London, N1 9DA
Become a member
How do you make sure that the softwood doesn’t warp – even if you get wood that isn’t warped in the first place?
The question was:- “how do I overcome the possibility of the soft wood warping.”
I have built over a 100 ft of baseboards using this technique and there has been no problem with warping. Now I always buy the timber from Watford Timber but previously I used B&Q and there was no problem with either supplier. I usually use far eastern ply. It is much cheaper than birch, though birch is nice to use.
I think the reason for the stability is the combination of plywood and softwood.
In fact the main structure is plywood with the softwood used to assist in making the joints.
All the surfaces between the two materials are joined using PVA glue and then either nailed or screwed.
The sides are made first . They consist of a strip of 6mm ply with the longitudinal lengths of softwood fixed along the top and bottom edge. Thus creating a channel section. The cross pieces including the two ends are then cut from 18 mm ply such that their width is a good fit between the two softwood strips. The cross pieces are fixed by screws through the softwood strips into the 18mm ply. This makes a rigid structure, When doing this care must be taken to keep every thing Square. Sometimes I use jigs to hold sections in place while fixing , if I am making several similar boards.
The top which is usually 6mm ply is the glued and pinned in place. Because of the width of the softwood (44×18) there is a relatively large surface area for the glue which ensures that the top holds every thing rigid and square. Prior to fixing the top, strips of soft similar in section to the longitudinals, are screwed to the top of the cross pieces, so the the top is supported fully. Gaps can be left in these support strips in order to allow room for cables to pass
So the combination of the ply and the softwood together with the design of the structure holds everything square and prevents warping. The depth of the side is usually 125 mm to allow for tortoise point motors, however even if you do not use these point motors I would not make it any less and the span should not exceed 4ft (1.2m)
I hope this explanation answers your question